Crucial to the advancement of metal additive manufacturing (AM) is the development of the proper simulation tools for ensuring repeatable, high-quality production from metal 3D printers. For that reason, we’ve seen a great deal of research and, more recently, commercial activity related to simulation tools for metal AM.
Most recently, e-Xstream engineering, part of Hexagon’s Manufacturing Intelligence division, has announced the creation of a suite of tools for enhanced simulations, including the evolution of metal microstructures with the IMDEA Materials Institute in Spain, which will aid a wide variety of advanced manufacturing technologies, including AM. This partnership aims at extending the footprint of e-Xstream ICME platform toward metallic materials and their associated manufacturing processes. To learn more, we spoke to members of IMDEA and Hexagon’s e-Xstream and Simufact teams.
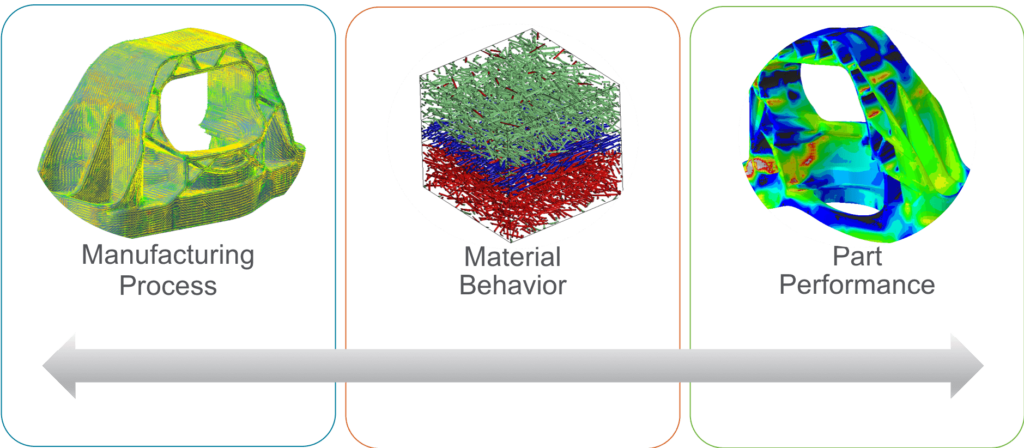
A diagram of how ICME modeling can be applied to additively manufactured parts. Image courtesy of Hexagon.
The partnership between IMDEA and e-Xstream is seeing models IMDEA is developing for metals incorporated into e-Xstream software, not just at the macroscale but at the microscale as well. The basis for this method is Integrated Computational Materials Engineering (ICME), which bridges the previously siloed fields materials engineering, design and manufacturing and testing, to make it possible to optimize parts in ways that takes all of these diverse areas into consideration. Javier Segurado, ICME Research Programme Leader at the IMDEA Materials Institute, explained:
“ICME is a big phrase that has been used in the world of materials for many years. The aim is to have simulation tools that join the properties of a microstructure with the properties of a given material. The ‘e’ in engineering [in ICME] represents the objective to integrate simulation tools within the production of a part.”
The end result is the ability to simulate the microstructure of a material and see that impact the macrostructure and overall behavior of the larger part. ICME of polymer-based materials acts as the backbone for e-Xstream and IMDEA is now developing solutions for ICME of metallic materials that will see some of the elements from IMDEA for metals incorporated into a variety of Hexagon software tools within e-Xstream’s broader 10X ICME solution.
Ralph Bernhardt, Director of Technical Sales for Hexagon’s Simufact business, described the high degree of specificity the technology is able to simulate and its impact on the effective properties of a part or component:
“We start with atomic length scales. Then, we investigate the scales in the nano- and micrometer area as the properties of a macroscopic component are triggered by effects that happen in much lower length scales. A challenge for the ICME approach is to connect all of the different length scales and make such sophisticated models from the nano- and the atomic length scales applicable to a macroscopic component. That’s the challenge. And this is what we are trying to achieve with our collaboration to bring together all these tools and to form this kind of solution platform.”
The applications described above have obvious implications for metal AM, which, as it currently stands, is still struggling to overcome issues related to repeatability and quality output. Up until recently, the vast majority of metal 3D printing has relied on a crude trial-and-error approach, in which a part would be printed seven or more times using various orientations, support strategies and process parameters. This, in turn, would result in a great deal of wasted material and, thus, high costs.
To tackle these problems, we’ve seen a variety of solutions enter the market. Systems manufacturers are incorporating an increasing amount of monitoring equipment into their machines in order to track and control for process errors. Sigma Labs has developed its own module that companies can incorporate directly into their machines if their own quality control hardware has not been sufficiently developed, as well.
Velo3D attempts to manage all aspects of the build process, including the aforementioned sensors and other hardware for process control, as well as tight maintenance of the ambient build environment. Perhaps most importantly, the company uses a simulation software to predict and compensate for potential issues in the build, such as warping or residual stress. A built-in feedback control loop then allows Velo3D machines to address issues during the build process, aiming for consistent repeatability.
Laurent Adam, R&D Director for e-Xstream engineering, described how the tools could be first used for powder bed fusion (PBF)—the technology that holds the greatest share of the metal AM market and where simulation technology is of the greatest focus. He began by saying how materials could be developed for PBF, with the proper powder atomization parameters. Then, printing conditions can be explored, simulating the way that powder is processed and reacts to an energy source, how it melts and cools.
“This phase transformation from powder to liquid to solid will have an impact on the local properties and will change the properties of the material during the processing. ICME looks exactly at how do we change the microstructure during processing and what is the response of the material in terms of its properties? The workflow that we have in mind is that we can start running such simulations on our ICME platform at low length scales according to need,” Adam said.
Segurado from IMDEA elaborated on how these microscopic changes have profound impacts on a printed object:
“Even if you see a part at the macro scale that has a good shape—even if you don’t see porosity—you can have properties that are absolutely different to what you thought. So, something that should behave the same way in two directions of the part, may subsequently be anisotropic because during the cooling period all of the grains from the liquid have grown in one direction. Thanks to the software that we are developing, you can account for this. Without doing a test on a particular part and a particular small element of a part, you can know a priori, through simulation, how it will behave, how this microstructure will impact the real properties that this will have.”
Simulation, thus, plays an important role in this regard and is likely why ANSYS acquired 3DSIM, adding the Louisville startup’s metal 3D printing simulation technology to its own portfolio of simulation products. The big difference between what Hexagon is developing and what ANSYS has publicly released is that these ICME tools are aimed across the entire process chain.
Adam concluded by pointing out that the use of simulation software to address the aforementioned issues clearly has an impact on time-to-market and the speed of production:
“To go into larger volume production, we need to increase these build rates. But if you change the processing parameters, if you speed up the build rate, you will get another microstructure and this will have an impact on part properties and performances. So ICME is dedicated to find out what the impact is of having a higher productivity with new technologies and how does it influence part performance.”
Subscribe to Our Email Newsletter
Stay up-to-date on all the latest news from the 3D printing industry and receive information and offers from third party vendors.
You May Also Like
Precision at the Microscale: UK Researchers Advance Medical Devices with BMF’s 3D Printing Tech
University of Nottingham researchers are using Boston Micro Fabrication‘s (BMF) 3D printing technology to develop medical devices that improve compatibility with human tissue. Funded by a UK grant, this project...
GaeaStar and Verve Coffee Roasters Start Pilot Production of Sustainable 3D Printed Coffee Cups
Following a 2022 debut in Germany, GaeaStar, a startup based in San Francisco and Berlin, has begun US pilot production of its sustainable, disposable clay cups and bowls made with...
Meltio and Accufacture Unveil Robotic Metal 3D Printer Made in the US
Meltio has partnered with Michigan-based robotics firm Accufacture to introduce Alchemist 1, a robotic cell designed for wire-laser metal 3D printing made in the US. This new system represents a...
WASP Highlights Advances in Healthcare 3D Printing at Italy’s Exposanità 2024
WASP takes center stage at Italy’s leading healthcare expo, Exposanità 2024, demonstrating the transformative impact of its advanced 3D printing technologies on the medical sector. Known for its line of...